WINNIPEG, MB: On May 11, 2023, Quik-Therm, a Winnipeg-based insulation technologies developer, hosted a local tour and presentation to showcase..
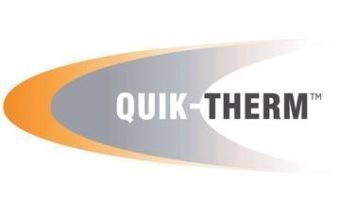
WINNIPEG, MB: On May 11, 2023, Quik-Therm, a Winnipeg-based insulation technologies developer, hosted a local tour and presentation to showcase..
WINNIPEG, Manitoba: On October 5, 2022, Winnipeg-based Quik-Therm Insulation was announced as one of the inaugural recipients of Efficiency Manitoba’s..
WINNIPEG, Canada – Quik-Therm, an innovative and forward-thinking designer and manufacturer of residential and commercial insulation systems, based in Winnipeg,..
WINNIPEG, Canada – Quik-Therm, a locally owned and operated development and design insulation technology company, based in Winnipeg, Canada, is..
The following test method relies on simple physics to illustrate how two completely different insulation systems – rigid Mineral Wool..
Over the past 14 years I have been fortunate to work with some of the finest building science organizations. As..
WINNIPEG, Canada – Quik-Therm, a locally owned and operated development and design company based in Winnipeg, Canada, is proud to..
An insulated hot, unvented roof system is an assembly that incorporates all of it’s thermal performance (insulation) above the roof..
When it comes to designing commercial insulated metal roofing systems for non-vented cathedral style, mono-slope and steel framed roofs in..